Производство каменного SPC ламината Steinholz находится на одной из самых крупных и современных фабрик, которая успешно занимается производством напольных покрытий уже более 20 лет. Чтобы снизить процент брака до абсолютного минимума, мы внедрили практику регулярного контроля производства и конечного качества продукта, которая включает непосредственное наблюдение со стороны европейского менеджмента компании Steinholz. В этой статье мы уделим внимание именно проверке готового покрытия.
Готовая продукция проверяется по 19 качественным признакам:
Готовая продукция проверяется по 19 качественным признакам:
1.Износостойкость верхнего защитного слоя проверяется с помощью Табер Теста. Напольное покрытие закрепляется на площадке, на поверхность ставится насадка со специальным абразивным материалом. Насадка совершает круговые возвратно-поступательные движения с контролируемым нажимом. После определённого количества оборотов проверяется насколько уменьшился верхний прозрачный защитный слой. Таким образом определяется стойкость напольного покрытия к абразивному износу защитного слоя. В случае с SPC ламинатом Steinholz после 25000 оборотов защитный слой уменьшается всего на 20%. Для сравнения, ламинат на HDF основе выдерживает только 4-6 тысяч оборотов до полного стирания поверхности до основы.
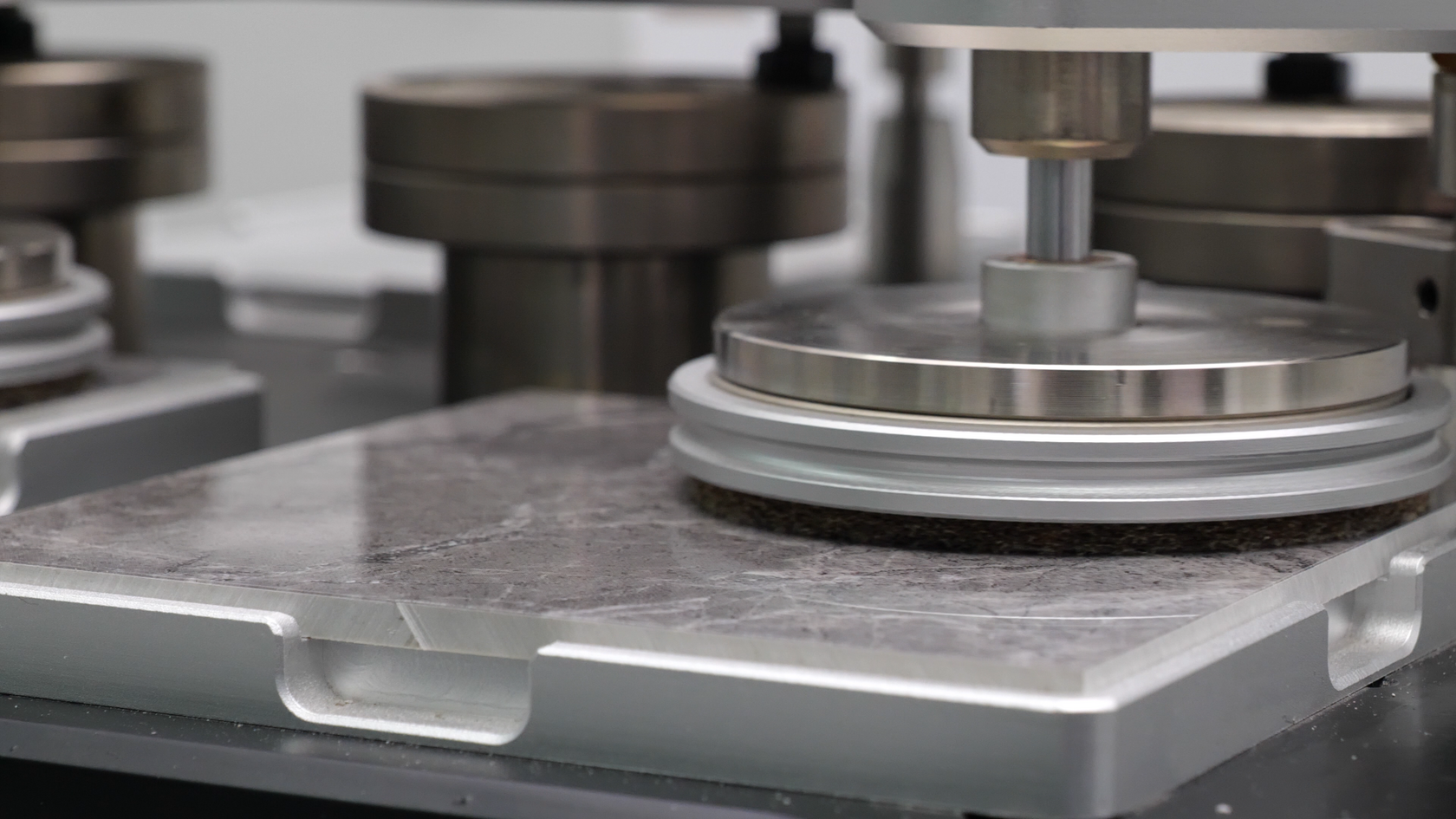
2. Стойкость к воздействию стульев на колесиках проверяется на специальном станке, который имитирует долговременную динамическую нагрузку стула на колесиках с человеком весом 100 кг. После нескольких тысяч циклов, проверяется износ и состояние замковых соединений напольного покрытия.
3. Проверка прочности диффузионного соединения слоев происходит на разрывном станке, где процесс разрыва производится с измерением усилий разделения слоев. Проверка показывает, что верхние слои покрытия мощно соединены с SPC основой покрытия.

4. Прочность замкового соединения на разрыв проверяется на специальном лабораторном станке. При испытании измеряются предельные усилия, при которых замок теряет свою конструкционную целостность.
5. Термостойкость напольного покрытия проверяется в камере с контролируемым нагревом. При постепенном нагреве до 150 градусов исследуются изменения геометрии испытательного образца. До 80 градусов видимых изменений формы и свойств образца Steinholz не наблюдается.
6. Этот пункт включает в себя 4 теста. Регулярно путём отбора выпускаемых планок и проведением комплекса высокоточных измерений специальными приборами проводится контроль стабильности геометрических размеров планок, . Проверяется 4 геометрических параметра: прямоугольность, косоугольность, скручивание планки и толщина планки. Такие регулярно проводимые измерения гарантируют беспроблемный монтаж планок в паркетное поле, без щелей и без затруднений.
7. Точность параметров нарезанного профиля замка проверяется на лазерном измерительном станке, который проверяет идеальное соответствие профиля эталонного шаблона с профилем отобранной с поточной линии планки.
8. Ультразвуковое исследование образца на отсутствие в теле планки воздушных каверн и прочих неоднородностей проводится в камере ультразвукового контроля.
9. Поверка в климатической камере на стабильность характеристик образца и паркетного поля с помощью искусственного старения под действием циклов нагревания, повышения влажности и дневного света.
10. Проводятся испытания на соответствие эталону матовости поверхности.
11. Проводятся испытания на соответствие цвета декора эталонному образцу соответствующего декора.
12. Визуальный контроль на отсутствие посторонних включений в верхнем защитном слое.
13. Обязательно проводятся исследования на подтверждение соответствию плотности прессования основы.
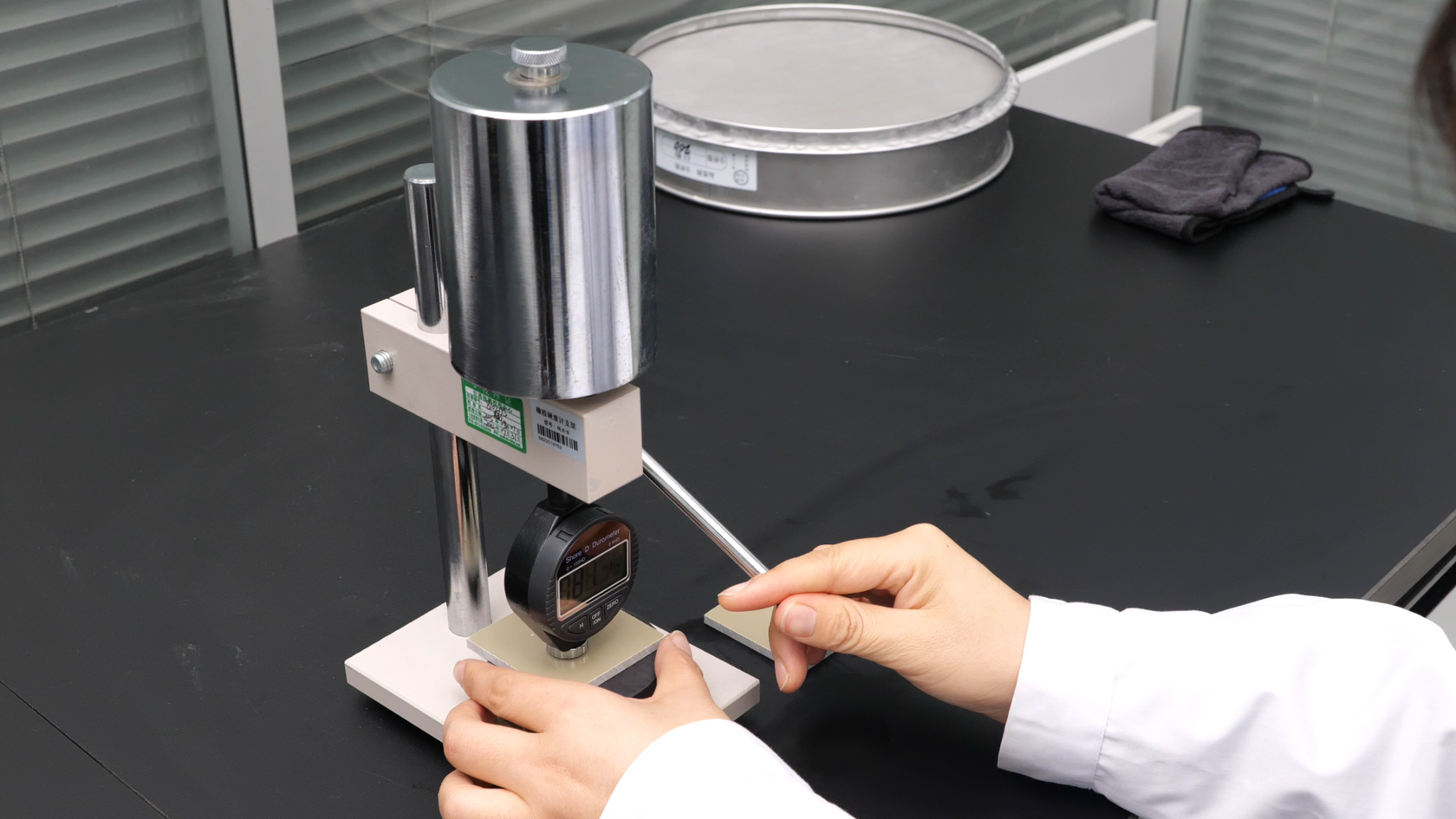
14. Проводится определение остаточной деформации поверхности при контролируемом давлении конуса на поверхность планки.
15. Проводятся испытания на светостойкость в камере с ультрафиолетовым облучением образца.
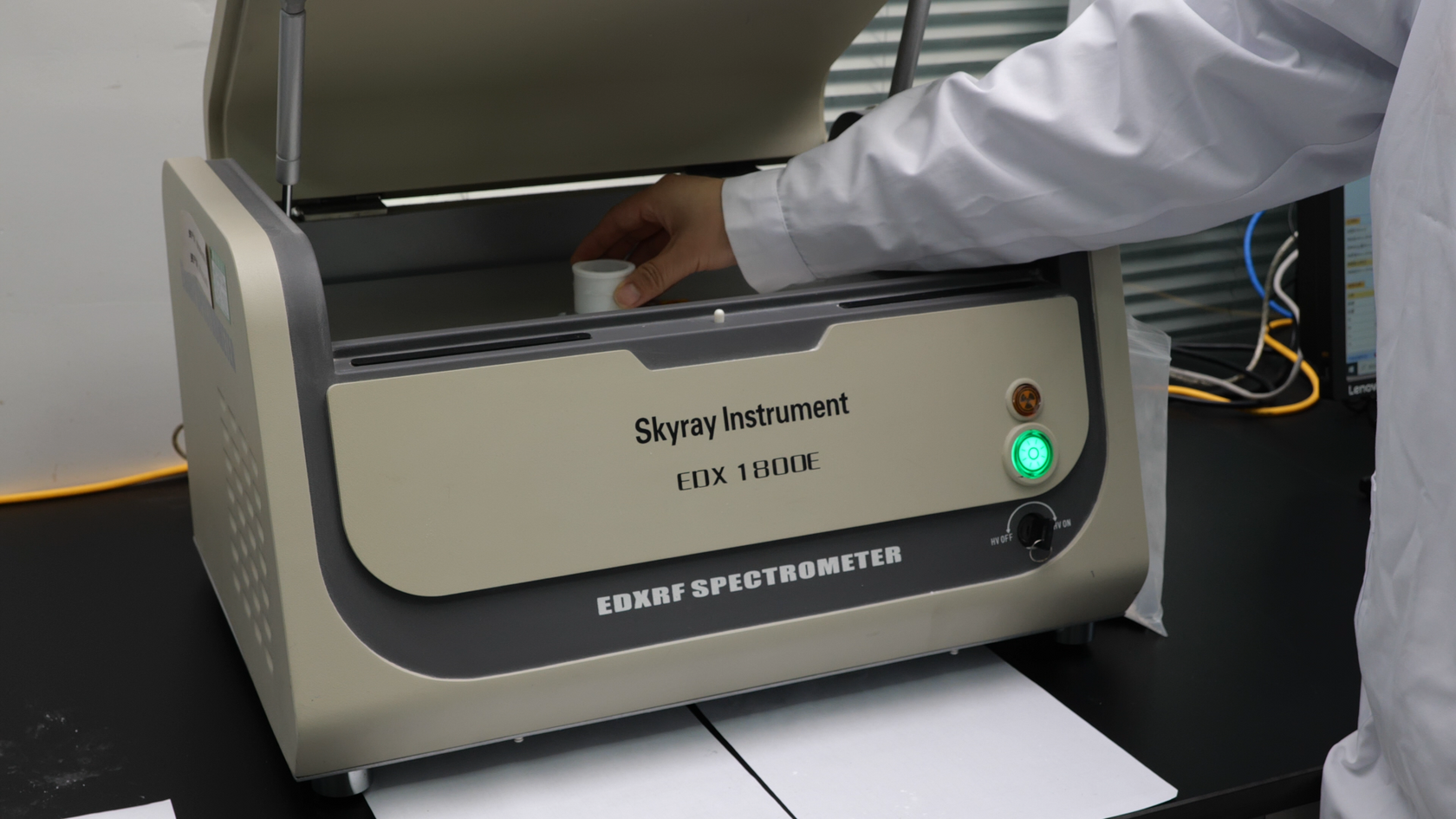
Кроме этого, согласно стандарту ISO 9001 на производстве проводится тщательная проверка сырья и его характеристик для поддержания стабильности качества продукции.
На производстве идет отбор и хранение планок из каждой партии в течении года, для того чтобы всегда быть готовыми к доказательству качественности продукции.
На производстве идет отбор и хранение планок из каждой партии в течении года, для того чтобы всегда быть готовыми к доказательству качественности продукции.